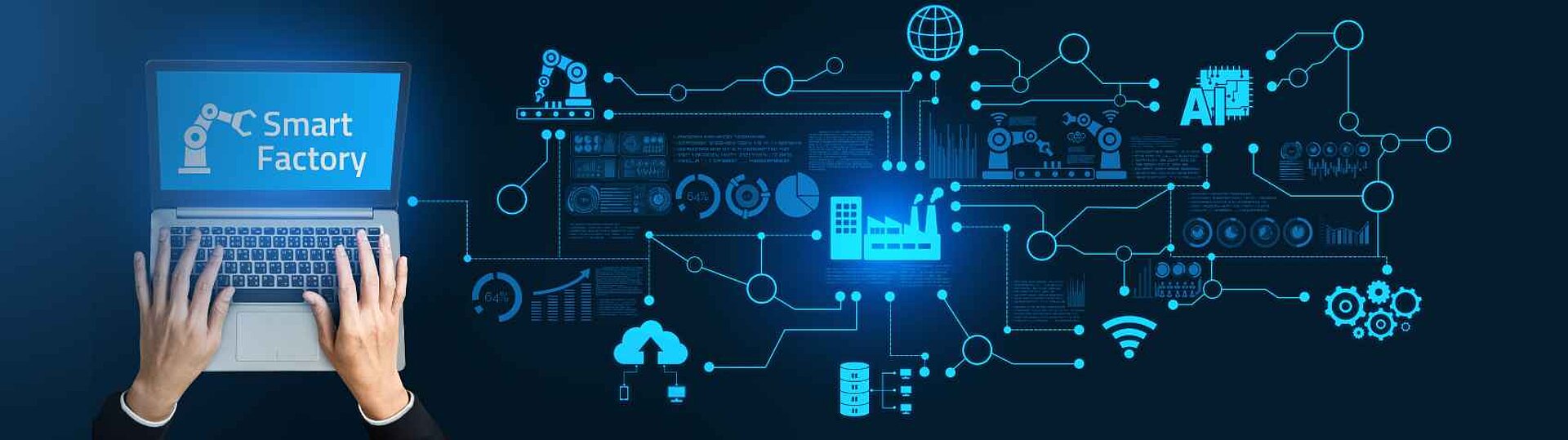
Find out how you can digitize your production
with solutions from MPDV!
Manufacturing Integration Platform / MIP – Smart Factory Glossar
The Manufacturing Integration Platform, or MIP for short, is an open platform for manufacturing. The integration platform was introduced by MPDV in 2018 and serves as a central information and data hub in production. The MIP, which is a semantic platform, provides an open link between the shop floor, manufacturing IT applications and the ERP system. The MIP incorporates all processes associated with production. All applications communicate with each other using a common information model, thereby ensuring full interoperability, no matter how dissimilar each application may be.
Customers using the MIP Integration Platform have the option of configuring a system that exactly meets the requirements of their production. Users are not tied to a single vendor: They can combine apps (mApps) from different manufacturers on the MIP. Consequently, the vendor lock-in effect that was common in the past is eliminated.
Examples for MIP applications
Since an mApp consists of anything that communicates with the MIP via the services offered, the applications are very diverse. For example:
- A machine control system uses PLCs to retrieve data of orders currently logged on to the machine and displays the data on the integrated operator display.
- A planning application from an ERP package analyzes pending orders and operations, puts them in the best possible sequence, and then uploads it to the MIP with updated schedules.
- A mobile app for smartphone or tablet accesses the MIP data, generates KPIs and visualizes them on dashboards.
MIP Marketplace and MIP Ecosystem
The MIP Marketplace is similar to an app store, where the user can download the required applications. Here you can find not only all mApps from MPDV, but also applications from third-party providers. Companies look for mApps that best meet their specific requirements. Even if the mApps from the different providers cover a similar range of functions, they differ in nuances.
All partners who offer their applications on the MIP Marketplace, belong to the MIP ecosystem, which is growing steadily. About fifty companies are currently part of the MIP ecosystem. Manufacturing companies can also develop their own applications thanks to the Software Development Kit (SDK) and operate them as an individual standard solution. Because the Manufacturing Integration Platform already provides the data structures and basic functions, companies save time and costs in the process.
Platform-based MES HYDRA X and APS FEDRA
The Manufacturing Execution System (MES) HYDRA X and also the Advanced Planning and Scheduling System (APS) FEDRA use the MIP as the basis. This has the advantage that companies can opt for exactly the MES and APS functions they need. If further mApps should later prove to be useful, they can be easily connected at any time.
The manufacturing apps from MPDV cover the entire functional scope of manufacturing management systems defined in VDI Guideline 5600 and actually go far beyond it. Each manufacturing app can be assigned to a specific area according to the Control loop "Smart Factory Elements". MPDV has also thematically grouped all mApps of MES HYDRA X and APS FEDRA into categories.
The manufacturing apps of MES HYDRA X are assigned to the following categories:
mApps from the Order Management category are the basis for the entire production control. They create the transparency needed to know in real time which product is being produced at which time and at which workplace. Furthermore, they highlight how far the order has progressed and whether there were any interruptions during the manufacturing process. Much of this data falls within the range of shop floor data collection.
- Work Order Management
- Work Order Execution
- Work Order Controlling
- AI-based Setup Time Prediction
- eKanban
- Project Time Management
mApps from the Resource Management category focus on any type of resource – from machines to tools and test equipment to any form of energy such as power, gas, or compressed air. Machine data collection, which is implemented in HYDRA X with the mApp Machine Monitoring, can also be found in this area.
- Shop Floor Monitor
- Machine Monitoring
- Machine Status Analysis
- AI-based Capacity Utilization Analysis
- Machine Performance KPIs
- Equipment Management
- Maintenance & Service Management
- DNC & Setting Data
- Process Data Management
- Production Process Analysis
- Energy Management
mApps from the Material Management category provide the right material in the right quantity and the right quality at the right place at the right time. Seamless tracking can also be realized using mApps from this field.
- Material & Inventory Management
- Tracking & Tracing
- Intralogistics & Packaging
mApps from the Assembly Management category efficiently map complex workflows within a production line. It also includes an application that can be used to implement video-supported operator guidance.
- Operator Guidance
- Production Process Modeling
- Assembly Control
mApps from the Quality Management category cover all aspects of product and process quality. They offer the necessary range of functions to map comprehensive quality assurance.
- Inspection Planning
- In-production Inspections
- Incoming Goods Inspection
- Supplier Evaluation
- Quality Analysis & Statistics
- Complaint Management
- FMEA
mApps from the HR Management category provide efficient personnel management - from flexible employee scheduling to payroll.
- Workforce Management
- Time & Attendance
- Personnel Time Management
- Incentive & Premium Wage
mApps from the Information Management category are aimed at the systematic digitalization of information and ensuring transparent and efficient communication.
- Digital Production Meeting
- Digital Checklist
- Shop Floor Messaging Service
- Measure Management
- Workflow Management
FAQ: Frequently asked questions about the Manufacturing Integration Platform
Do you have questions about the integration platform MIP? We have the answers! If you require further information, do not hesitate to contact us!
The integration platform MIP has a common, uniform and integrating information structure. This means that all systems speak a uniform language that is used to exchange information on the current status of production flexibly with each other. Each recorded value has a defined meaning. Applications and users alike therefore know whether a piece of information is about scrap, downtime, or temperature. The MIP guarantees that each application accesses the latest data. All data recorded in the shop floor, as well as the master data, is contained in the core of the MIP, the Virtual Production Reality (ViPR).
The video explains the basics of the MIP integration platform and illustrates how it works.
Manufacturing processes are becoming increasingly complex. That is why companies today demand flexible platform solutions that can be used to combine applications from different providers or to customize applications themselves to suit their individual needs. The MIP from MPDV makes exactly this possible. The platform integrates different systems used in manufacturing. This is vital for the survival in the age of Industry 4.0, where the number of systems is constantly growing. Only when machines and plants automatically exchange information and speak one language will the vision of a Smart Factory, that is, a self-regulating factory, become reality. The challenge is that as the number of systems increases, so does the number of interfaces. The integration platform MIP facilitates the integration of all systems without having to implement countless interfaces. Systems from different providers can therefore interoperate with each other entirely without knowing each other or having to adapt to one another.
IoT platforms can be used to collect, store, and analyze large amounts of data. The difference to the Manufacturing Integration Platform (MIP) is not only evident in name. Applications from different providers can share information with each other via the standardized object model of the MIP. Details on specific objects like machine, tools, or material are stored in the model. All applications of the Manufacturing Integration Platform access it and have thereby the same database and a uniform level of information. The MIP also differs from an IoT platform in this respect: Usually, IoT platforms are technology platforms that only manage data. In contrast, the MIP is a semantic platform with a focus on content. With the MIP, users can create an image of production reality that can be used by all mApps.
The Manufacturing Integration Platform can be operated in two ways:
Operating in the cloud allows companies to focus on their core business and offload numerous IT tasks to the cloud service provider. MPDV handles the server-side operation of manufacturing IT in the cloud with Smart Factory Cloud Services. Companies do not need their own infrastructure or MIP expertise to use this Software as a Service (SaaS) solution.
Manufacturing companies can also operate the MIP integration platform on-premise. In doing so, companies may choose between operating one or more centralized instances for different plants or operating local instances at each site. From a technical point of view, operation as a central instance is similar to operation in the cloud, although in this case the company operates the cloud itself. It also means that the entire infrastructure required to operate the MIP is then deployed and maintained by the company.
Before selecting an operating model, companies should shed light on the following drivers:
- Organizational conditions
- Scalability
- Availability
- Internet performance
- Assessment of corporate risks
Would you like more information? We are happy to help.
Just fill in the form below. We will take care of your inquiry promptly.