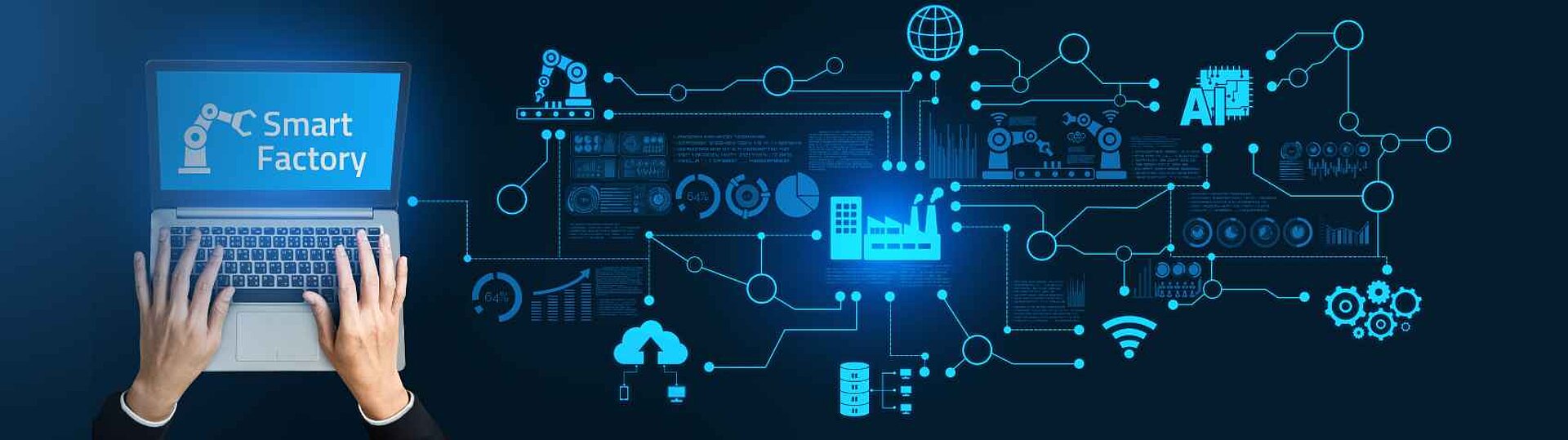
Find out how you can digitize your production
with solutions from MPDV!
Total Productive Management / TPM – Smart Factory Glossar
Total Productive Management (TPM) is an integrated Lean Management method. The paramount goal of TPM is to increase the overall equipment effectiveness of manufacturing companies. To this end, downtimes and failures are reduced, processes are presented transparently, and all company processes are regularly reviewed and optimized as part of the continuous improvement process (CIP). Total Productive Management involves all employees to achieve the greatest possible acceptance within the company.
Total Productive Management complements the Total Productive Maintenance concept. Total Productive Maintenance focusses on optimizing maintenance activities but does not integrate all stages of the production process. Total Productive Management is often used synonymously with Total Productive Maintenance.
Six pillars of Total Productive Management
The Fraunhofer Institute for Material Flow and Logistics IML has developed a TPM model consisting of six key pillars. Other models divide TPM into eight pillars, whereas the basic idea and contents are similar.
- Continuous improvement: Each employee is involved and encouraged to constantly optimize their workplace. This constant process results in the optimization of all business workflows.
- Shared production: Production and maintenance are integrated across divisions and not isolated from each other. Joint decision-making has a positive effect on both areas.
- Maintenance strategies: Various approaches (preventive, reactive, condition-based) should be combined into an integral concept. The efficiency of the concept is to be reviewed at regular intervals.
- Education and training: In order to safeguard the future, employees must have access to targeted training options to further develop their skills and respond appropriately and flexibly to new developments.
- Quality management: Predefined controls and checking mechanisms are necessary to ensure high quality of production on a permanent basis thus reducing scrap and rework.
- Life Cycle Management: Machines and production units must be operated in an economically sustainable manner. Investments should be checked for profitability on a regular basis.
TPM and MES
A Manufacturing Execution System (MES) like MPDV's HYDRA X supports manufacturing companies in their efforts to implement Total Productive Management.
- In the quality management sector an MES, for example, helps companies plan their inspection tasks consistently. The mApp In-production inspection digitally maps inspection steps, guides operators through quality assurance processes and documents inspection results.
- Applications like the digital operator guidance navigate employees step by step through the manufacturing process of products with a wide range of variants. Failure rates can therefore be reduced considerably.
An MES like HYDRA X correlates both consumption and performance values of machines with other production data. As a result, reliable key figures can be calculated that provide information about productivity or effectiveness of production units. The data collected can also be used to optimize maintenance strategies and to achieve higher availability.
Source
- Total Productive Maintenance: Wikipedia, 02 September 2021 [online] https://en.wikipedia.org/wiki/Total_productive_maintenance (requested on 22.03.2024).
Would you like more information? We are happy to help.
Just fill in the form below. We will take care of your inquiry promptly.